Generally speaking, we improve the rate performance of lithium-ion batteries by adjusting the selection of positive and negative electrode materials and formula adjustments, such as choosing ternary materials and NCA materials with higher ionic and electronic conductivity, and selecting small particle graphite materials for the negative electrode, or Li4Ti5O12 with a larger Li+diffusion coefficient. By increasing the amount of conductive agent for carbon black, we can reduce the impedance and polarization of the electrode and improve the rate performance of lithium-ion batteries. In fact, the selection of less focused current collectors can also have a certain impact on the rate performance of lithium-ion batteries.
Generally speaking, the positive electrode of lithium-ion batteries uses Al foil, and the negative electrode uses Cu foil as the current collector. The main function of the current collector is to conduct electrons from the active materials of the positive and negative electrodes. Ordinary Al foil is made by mechanically rolling pure Al to 10-30um, with a relatively smooth surface. Therefore, the contact area between the active material and the Al foil is small, and electronic conduction between the Al foil and the active material may become a limiting factor during high rate discharge. Recently, Chang Uk Jeong (first author) and Kuk Young Cho (corresponding author) from Gwangju National University in South Korea used electrocorrosion to create an uneven surface on originally smooth Al foil, increasing the contact area between LCO material and current collector, improving adhesion, reducing polarization and contact resistance during charge and discharge processes, and significantly improving the rate performance and cycle life of lithium-ion batteries.
The treatment process used by Chang Uk Jeong is shown in the figure above. Firstly, a 30V constant voltage power supply Al foil is used for electrolytic oxidation treatment for 10 minutes to form a thick layer of Al2O3 on the surface of the Al foil. Then, chromium oxide CrO3 and H3PO4 are used for corrosion for 18 hours to remove the Al2O3 on the surface and form an uneven surface on the surface of the Al foil.
After oxidation corrosion treatment, Al foil usually shows a certain degree of strength reduction. In Figure a, Chang UkJeong compared the tensile strength of untreated Al foil, 30V oxidation for 5 minutes, and 30V oxidation for 10 minutes. It can be seen that the tensile strength of untreated Al foil reached 245MPa, while the strength of Al foil after 5 minutes of oxidation treatment and corrosion decreased to 235MPa. Further increasing the oxidation treatment event to 10 minutes, the tensile strength of Al foil decreased to 227MPa. The decrease in tensile strength of Al foil is mainly due to the damage of some Al by the oxidation corrosion treatment process. This can be seen from the change in the thickness of the Al foil. From Figure b, it can be seen that the untreated Al foil has a thickness of 11um. After 5 minutes of treatment, the thickness decreased to 10.4um, and after 10 minutes of treatment, it decreased to 9.9um. Although the strength of the processed Al foil has decreased, the tensile strength of 227-235MPa can fully meet the requirements for the strength of Al foil during coating and winding processes.
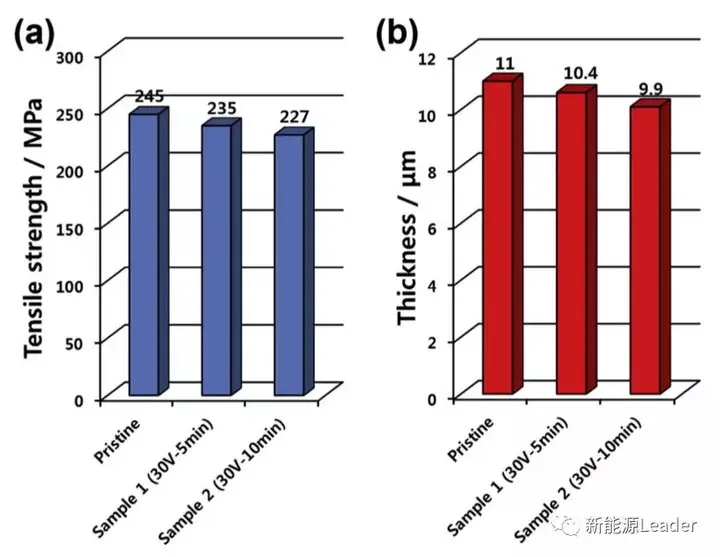
The XRD analysis of the surface of Al foil (as shown in the figure below) indicates that the surface of Al foil is mainly composed of cubic structured metal Al, and no diffraction peaks of alumina were found. This indicates that the Al oxide formed in the first step of anodizing treatment has been completely removed in the subsequent CrO3 and H3PO4 corrosion treatment. This ensures good conductivity on the surface of Al foil, which is of great significance for reducing the contact impedance between the active material and the current collector, and reducing electrode polarization.
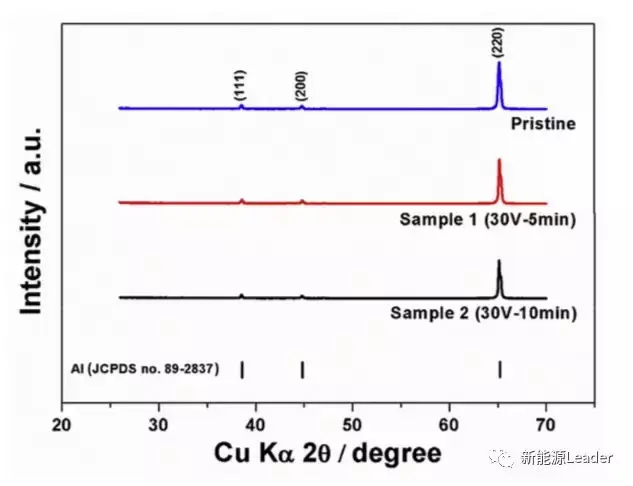
After oxidation corrosion treatment, the surface of Al foil presents a honeycomb structure, which is mainly formed by the corrosion of the anodized layer on the surface of Al foil. The diameter of these honeycomb structures is closely related to the voltage and time of anodizing treatment. Increasing the anodizing voltage and treatment time will lead to an increase in the diameter of these honeycomb structures. At the same time, we also observed that with the increase of anodizing treatment time and anodizing voltage, the contact angle between water and Al foil showed a decreasing trend, indicating an increase in the hydrophilicity of Al foil.
Atomic force microscopy is more sensitive to the surface roughness of materials. Chang Uk Jeong observed ordinary Al foil and treated Al foil through atomic force microscopy. The results are shown in the following figure. The surface of ordinary Al foil is relatively smooth, with a roughness of 3.41. After 5 minutes of treatment, the roughness of Al foil increased to 4.078, and after 10 minutes of treatment, the surface roughness of Al foil further increased to 4.98. At the same time, we can see from the figure that the surface of treated Al foil presents a mountain like protrusion, as observed in the SEM earlier.
The changes in surface morphology and roughness will ultimately be reflected in the impact on the rate performance of lithium-ion batteries. The author tested the electrochemical performance of the treated Al foil using LCO material. From Figure a, it can be seen that the capacity of ordinary Al foil, Al foil treated for 5 minutes, and Al foil treated for 10 minutes during the first charge were 184mAh/g, 183mAh/g, and 189mAh/g, respectively. The subsequent discharge capacities were 176, 175, and 180mAh/g, respectively. At the same time, we were able to observe a decrease in polarization of the treated Al foil, with voltage plateaus of 3.82V, 3.84V, and 3.86V, respectively, during the discharge process. In the cyclic test, the difference between the three is not significant, but a significant difference can be observed in the rate test. From the graph, it can be seen that when the current density is increased to 450mA/g, the treated Al foil shows a very obvious advantage. When the current density is further increased to 750mA/g, the discharge capacity of the ordinary Al foil electrode is only about 20mAh/g, while the Al foil treated for 10 minutes shows the best rate performance, with a capacity of 145mAh/g.
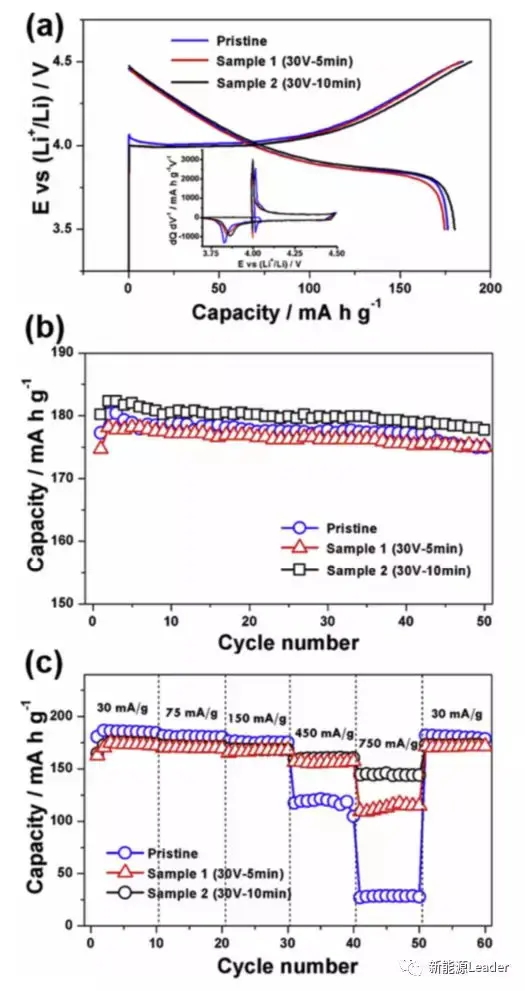
The main reason for the improvement in the rate performance of the processed Al foil is the decrease in contact resistance, which reduces the polarization of the battery during discharge. The following figure compares the relationship between the polarization resistance and discharge depth of the battery in the second and 20th cycles. It can be seen from the figure that the polarization resistance of ordinary Al foil is the highest, slightly lower after 5 minutes of treatment, and the lowest after 10 minutes of treatment, which is consistent with the previous rate test results.

Chang Uk Jeong prepared Al foil with uneven surface structure through a relatively simple anodizing corrosion treatment process. This process has little effect on the tensile strength of Al foil, but can significantly improve the adhesion between the active material and Al foil, reduce contact impedance, lower polarization, and effectively enhance the rate performance of lithium-ion batteries.
Author: Looking at the railing
Author: New Energy Leader
Source: First Electric Network (www.d1ev. com)
Special statement: This article was uploaded and published by the author of the "NetEase Account" on the NetEase self media platform, and only represents the author's views. NetEase only provides an information publishing platform.
Responsible Editor: Wang Hailu, NA1702